Литье по газифицируемым моделям. ЛГМ - процесс (предвспениватели полистирола, модельные автоматы ЛГМ, вибростолы, вакуумные системы, автоклавы и формовочные линии )
Литье по газифицируемым (выжигаемым) моделям из сополимера и пенополистирола
ЛГМ-процесс (Policast, Lost Foam Cast) - современная технология производства высокоточных отливок, позволяющих значительно уменьшить расходы на передел и снизить себестоимость готовой продукции. Пенополистирол относится к так называемым твердым пенам или ячеисто-пленочным дисперсным системам, которая в физической химии определяются как дисперсия газа в твердом веществе.
Метод литья ЛГМ: модель из сополимера или полистирола (пенопласта), полученная в модельных автоматах или автоклавах, покрывают противопригарной краской, засыпают песком в вакуумной опоке и накрывают полиэтиленовой пленкой для создания разряжения. Вакуумная опока подключается к насосу вакуумной системы. Производится заливка жидкого металла в форму и замещение расплавом пенополистирольной модели, которая испаряется в газ. Получаемая отливка имеет чистоту поверхности Rz40 до 7-ого класса точности.
Материалы отливок:
- чугун практически всех марки от СЧ15 до ВЧ50;
- стали от низко- и среднеуглеродистых низколегированных (с содержанием углерода от 0.20%) до высоколегированных, жаропрочных марок сталей и спецсталей;
- цветные металлы: медь, алюминий, бронза, латунь.
Преимущества технологии ЛГМ (POLICAST-process):
- Главные достоинства - возможность производства отливок высокой точности и качества при значительном снижение трудозатрат и себестоимости изготовления.
- Практически безотходное производство - примерно 97% песка повторно используется в системе пескооборота. Потери песка составляет всего 3%, которые складываются на отсев мелкой фракции, обеспыливание и потери в виде просыпи.
- Простая технология формовки без связующих компонентов и формовочных смесей. В технологии ЛГМ для формовки используется только песок.
- Высокая точность литья позволяет минимизировать затраты на финишную мехобработку или даже отказаться от нее.
- Используется для изготовления сложных и точных отливок, которые другими способами получить затруднительно. Очень выгодно эта технологии нашла применение для изготовления шнеков, корпусов, звездочек, головок и блоков цилиндров двигателей, художественных и другие отливок.
Этапы проектирования и изготовления комплекса ЛГМ:
- разработка технического задания на проектирование;
- проектирование и изготовление комплекса ЛГМ;
- проектирование и изготовление литейной оснастки;
- поставка оборудования;- монтаж и пусконаладка на площадке Заказчика;
- обучение персонала и запуск оборудования;- отработка технологии литья;
- ввод оборудования в эксплуатацию и постановка на гарантийное обслуживание.
Комплекс литья по газифицируемым моделям состоит из 2-х основных участков: «Белый цех» и «Черный цех». «Белый цех» - это участок изготовления пенополистирольных моделей, покраски и сушки модельных блоков. «Черный цех» - участок формовки и заливки модельных блоков, включающий линию формовки и систему пескооборота.
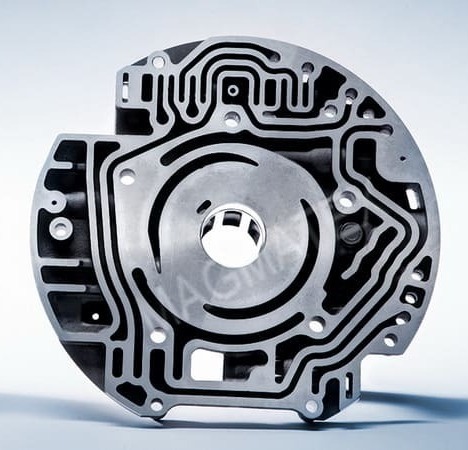
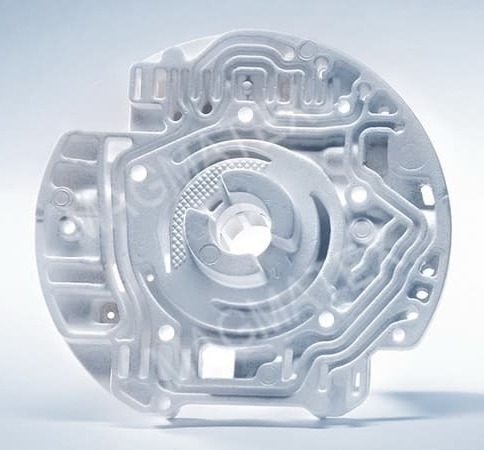
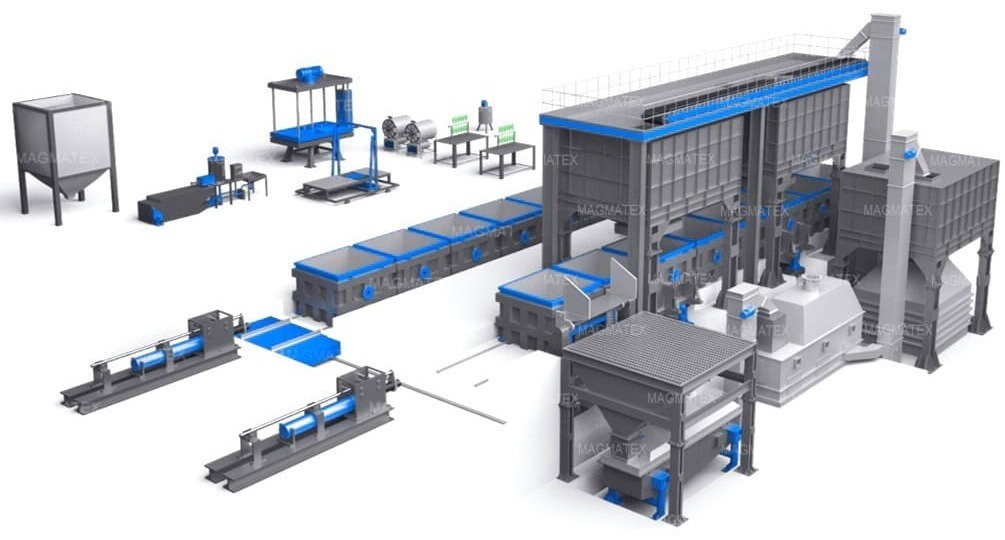
Equipment Lost Foam and Policast process MAGMATEX ЛГМ оборудование
Обработка видео...
Заполните форму и мы вышлем Вам коммерческое предложение на линию ЛГМ
БЕЛЫЙ ЦЕХ ЛГМ - производство полистирольных моделей (модельный участок ЛГМ)
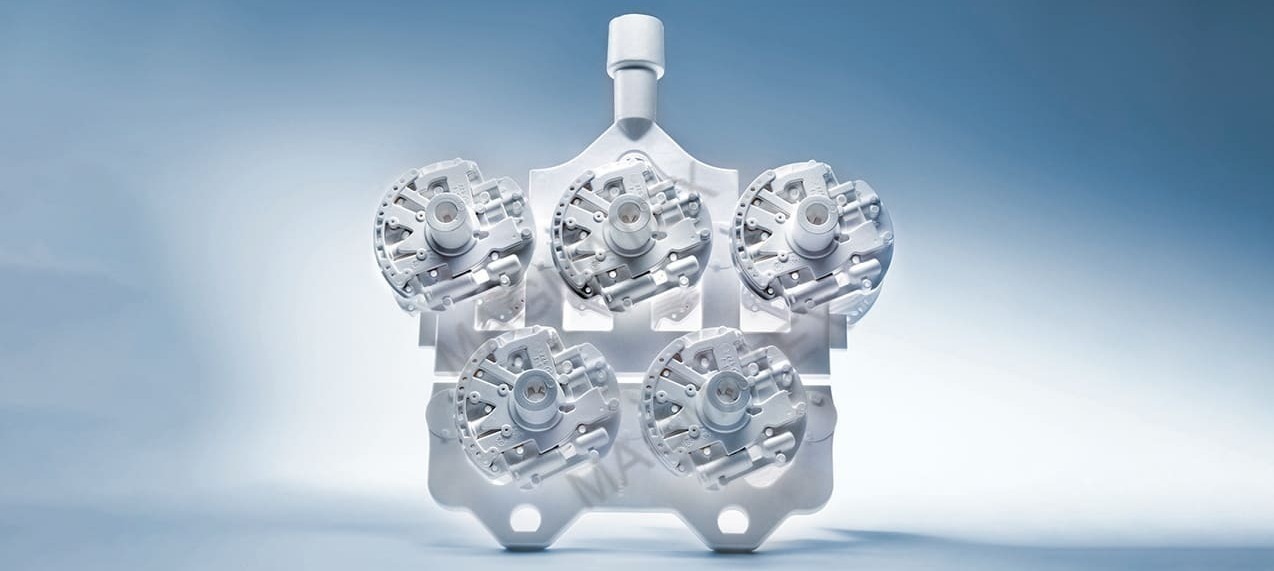
Технологические операции изготовления моделей ЛГМ: Предвспенивание полистирола → Изготовление пенополистирольных моделей → Склеивание моделей в блоки → Окраска блоков и сушка
Предвспениватель полистирола EPS с сушильной камерой (сушилкой)
Вспенивание гранул сополимера или полистирола производится в закрытой камере автоматического предвспенивателя. В качестве источника пара рекомендуется использовать парогенератор.
Управление предвспенивателем осуществляется PLC-контроллером, путем настройки подачи материала, количеством подаваемого водяного пара, давления в камере и времени вспенивания сырья.
Технология предвспенивания гранул исходного сырья производится путем подачи пара при температуре 90~110 оС. Под действием пара гранулы увеличиваются в объеме до заданной плотности. Время вспенивания составляет не более 90 сек. Далее вспененные гранулы из закрытой камеры попадают в сушильный блок, где в кипящем слое остывание и удаление остаточной влаги. Из сушильного блока вспененные гранулы, при помощи пневмотранспорта поступают в бункер хранения для их насыщение кислородом.
Технические параметры предвспенивателя EPS:
- Диаметр камеры вспенивания - 500 мм;
- Высота камеры вспенивания - 700 мм;
- Объем камеры вспенивания - 0,12 м3;
- Достижимая плотность гранул - 12-40 кг/м3;
- Производительность 40-160 кг/час;
- Необходимое давление воздуха - 2-3 атм.;
- Расход воздуха - 0,05-0,06 м3/цикл;
- Необходимое давление пара - 2-3 атм.;
- Расход пара - 0,8-1,0 кг/цикл;
- Время цикла - 1,5 мин;
- Размеры предвспенивателя - 1100х800х1500 мм;
- Мощность установки - 2,2 кВт;
- Масса установки - 500 кг;
- Производительность сушилки - 400 кг/час;
- Размер сушилки - 4400х1600х1100 мм.
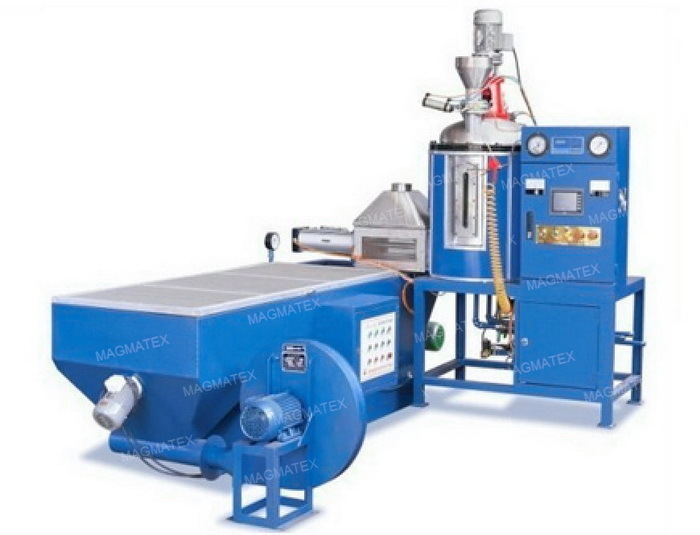
Полистирол литейный К910 Финляндия (аналог китайского полистирола А107)
Производитель - Финляндия. Цена - ПО ЗАПРОСУ руб за кг.
Фасовка в Биг-Бэгах . В наличии на складе.
Минимальная партия заказа - 1100 кг (Биг-Бэг - 1 шт.).
Вспенивающийся полистирол K910 используется для литейной промышленности и характеризуется высокой прочностью на деформацию, вибростойкостью, водонепроницаемостью, стоек к жирам, растворам кислот и щелочей. Гранулы полистирола обладает замкнутой ячеистой структурой на 95% состоящий из газов, которые используются в процессе вспенивания.
Основные свойства полистирола K910: Насыпная плотность 600кг/м3, фракция 0.4~0.7мм, вспенивающий агент 6-7% масс., минимальная достижимая плотность 15кг/м3, плотность формованного изделия 15-50кг/м3.
Пенополистирол К910 (Финляндия). Предназначен для изготовления тонкостенных моделей, путем предвсвспенивания гранул при температуре 100-110°C, вылеживания 6-24 часа и формования путем вторичного вспенивая в пресс-формах. Коэффициент усадки после вторичного вспенивания 1%. Служит для изготовления полистирольных форм на модельном участке, которые применяются в получении отливок методом ЛГМ (литье по газифицированным). Поставляется в "Биг-Бэгах" по 1100 кг. Всегда есть в наличии на складе.
Автоклавы литейные WS - YDA
Автоклавы служат для изготовления мелких и средних размеров моделей из пенополистирола. Изготовление моделей производится путем задува предвспененного полистирола в металлическую пресс-форму и подачи пара под давлением.
Операции по извлечению моделей, сборке (разборке) пресс-форм производится оператором вручную.Автоклав оборудован собственным парогенератором и имеет возможность подключаться также к внешнему источнику пара. Внутренние основные элементы рабочей камеры автоклава изготавливаются из нержавеющей стали.
Камера автоклава имеет выдвижной ящик, что упрощает процесс загрузки пресс-формы. Режим работы автоклава может регулироваться в пределах 0~60 мин и при температуре обработки 40-135 оС. Время обработки и давление в камере подбираются исходя из конфигурации получаемой модели.
Технические параметры литейных автоклавов WS-YDA:
Модель автоклава | WS-150YDA | WS-200YDA | WS-280YDA | WS-400YDA | WS-500YDA | ||||
Объем камеры, л | 150 литров | 200 литров | 280 литров | 400 литров | 500 литров | ||||
Размер камеры (Ø * H), мм | 440 * 1000 | 515 * 1000 | 600 * 1000 | 700 * 1000 | 700 * 1300 | ||||
Давление, МПа | 0.22 | ||||||||
Рабочая температура, °С | 40 - 105 -134 °С | ||||||||
Точность температуры, °С | ±1 °С | ||||||||
Мощность парогенератора, кВт | 9 KW | 9 KW | 12 KW | 18 KW | 18 KW | ||||
Размер, мм | 1400×600×1300 | 1400×670×1650 | 1400×770×1780 | 1430×880×1830 | 1800×900×1820 | ||||
Масса, кг | 240 | 260 | 365 | 420 | 470 |
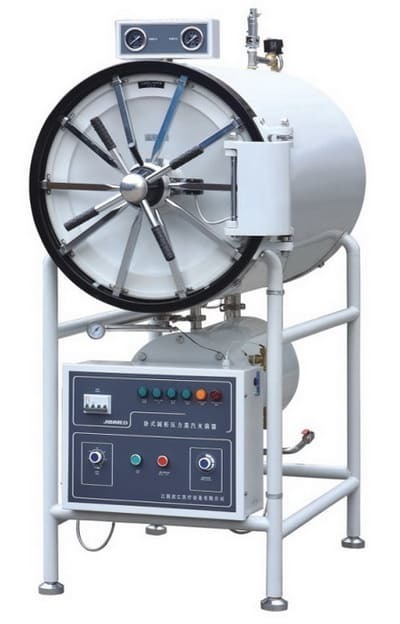
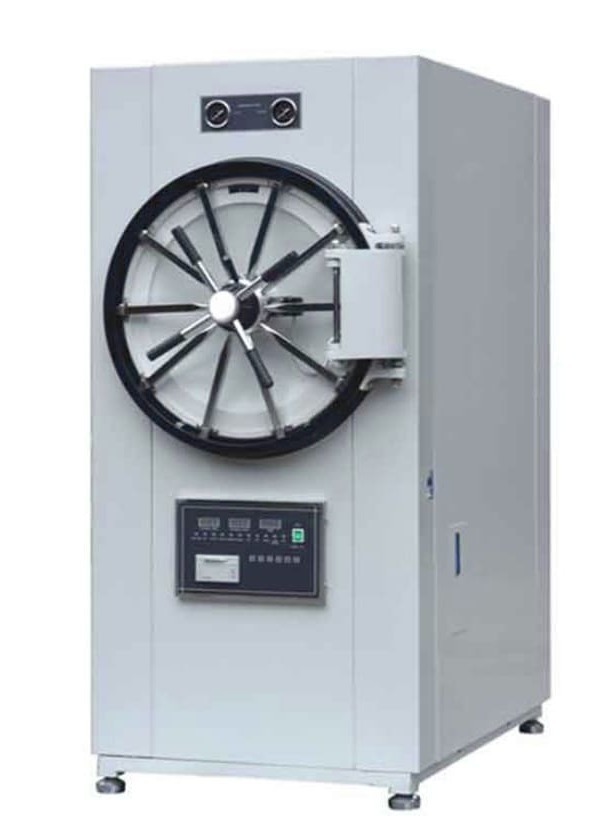
Автоклавы литейные WS - YDB с микрокомпьютерным управлением
Автоклавы WS - YDB аналог горизонтального литейного автоклава WS - YDA , только с дополнительным микрокомпьютерным управлением , служат для создания моделей из полистирола. Изготовление моделей производится путем задува предвспененного полистирола в металлическую пресс-форму и подачи пара под давлением. Рабочая температура в автоклаве 110-120 оС, позволяют достичь оптимального качества модели как снаружи, так и внутри.
Операции по извлечению моделей, сборке (разборке) пресс-форм производится оператором вручную. Автоклав оборудован собственным парогенератором и имеет возможность подключаться также к внешнему источнику пара. Система управления автоматически настраивается, обеспечивает надежный режим работы. Система управления автоматически регулирует вход и выход пара в соответствии с температурой камеры во время работы.
Технические параметры литейных автоклавов WS-YDB:
Модель | WS-150YDB | WS-200YDB | WS-280YDB | ||
Объем камеры, л | 150 литров | 200 литров | 280 литров | ||
Размер камеры (Ø * H), мм | 440 * 1000 | 515 * 1000 | 600 * 1000 | ||
Давление, МПа | 0.22 | ||||
Рабочая температура, °С | 40 - 105 -134 °С | ||||
Точность температуры, °С | ±1 °С | ||||
Мощность парогенератора, кВт | 9 KW | 9 KW | 12 KW | ||
Размер, мм | 1400×650×1600 | 1400×750×1700 | 1520×910×1900 | ||
Масса, кг | 340 | 350 | 460 |
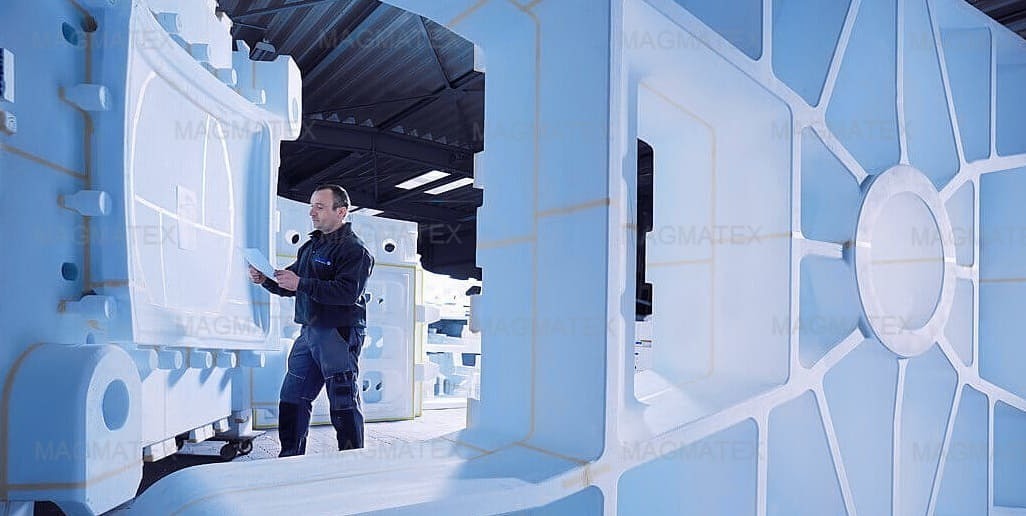
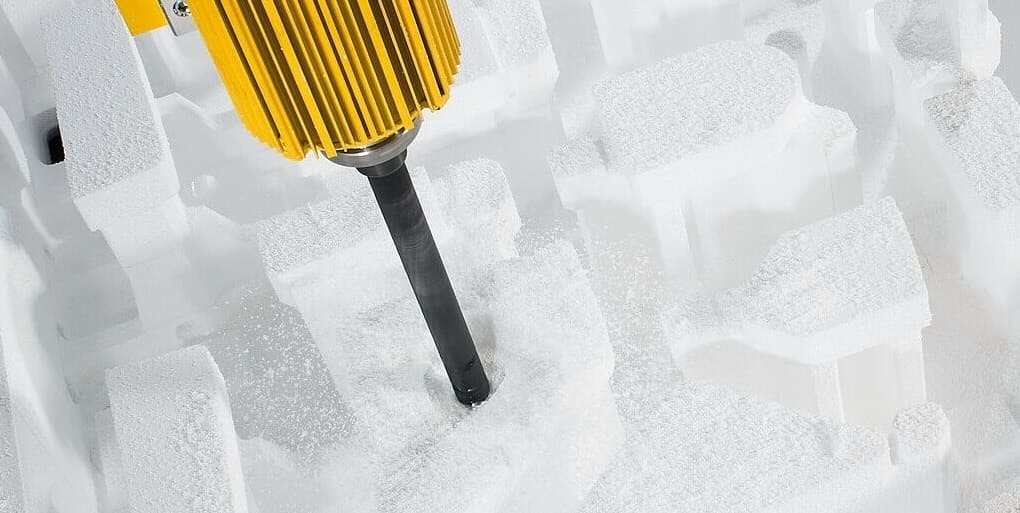
Станок СРП для резки моделей
Станок СРП служит для порезки пенополистирольных блоков по заданной с ПК программе. Резка блоков осуществляется нагретой струной из никель-хромового сплава на поворотном столе.
Нагрев струны станка производится электрическим током с регулировкой мощности накала. Скорость перемещения Ni-Cr струны регулируется в интервале 0~100 мм/сек. Резка производится в 2D и 3D режиме (на поворотном столе).
Станок для резки моделей"СРП-МАКСИ" Рабочее поле 2200*1100*1500мм, длина режущих струн 1500мм; мощность 1300Вт.
Станок (стол) для резки моделей «СПР-КОНТУР» Рабочее поле 750*490*1350мм; длина режущих струн 1350 мм; мощность 150Вт.
Краскомешалка
Краскомешалка КР5 – миксер, предназначенный для приготовления однородного противопригарного покрытия (краски). Загрузка компонентов краски осуществляется через верх, а выпуск через шаровой кран. Размер бака Ø600 * 500 мм. Мощность двигателя краскомешалки - 4 кВт. В бак с водой засыпается порошкообразный противопригарный порошок. Смешивание производится до получение однородной массы требуемой вязкости.Готовые модельные блоки покрывают противопригарным покрытием, после чего сушатся. После сушки окрашенный модельный блок готов к дальнейшей формовке.
Модельные автоматы для серийного производства
Модельные автоматы LWH (гидравлические) и EPS-C (винтовые - механические) служат для изготовления крупных или серийных моделей из пенополистирола. Вторичное вспенивание полистирола происходит в металлической (алюминиевой) пресс-форме под давлением.
Отличие модели LWH (гидравлические) от EPS-C (винтовые) более скоросной режим работы, который достигается за счет быстрого и плавного перемещения плит с пресс формой
Технология получения модели на автомате:
Пресс-форма крепится на плитах автомата и закрывается путем опускания верхней подвижной плиты до исходного положения.
Управлением автоматом производится с дисплея управления и ПЛК-контроллера. Производится инжекция предвспененного полистирола в металлическую пресс-форму, далее осуществляется подача пара и производится вторичное вспенивание полистирола.
Формирование модели происходит за 1~2 мин. По истечению заданного времени производится подача холодной воды, останавливающая остаточное вспенивание и охлаждающая пресс-форму во избежание оплавления модели. Производится раскрытье пресс-формы, продувка сжатым воздухом и извлечение готовой модели.
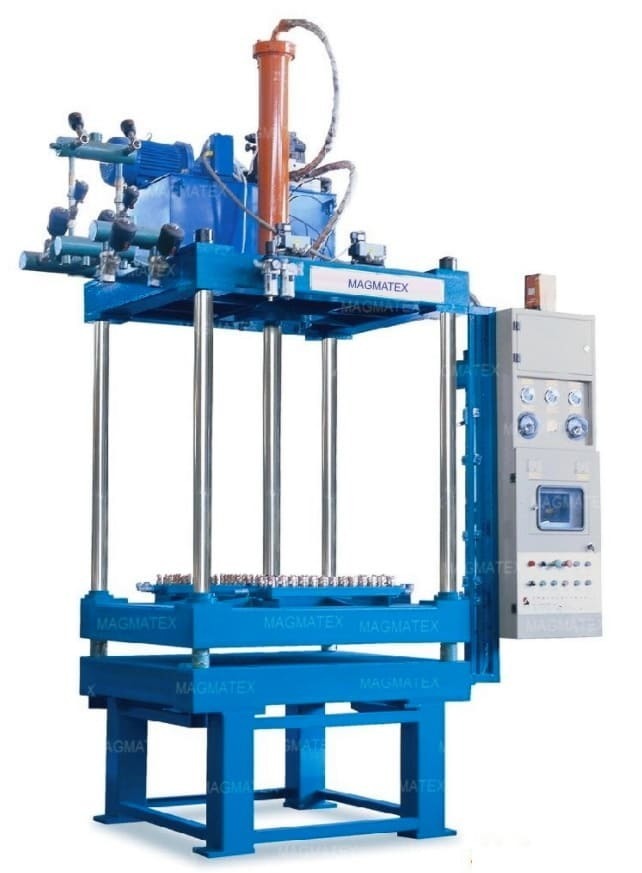
Модель | Тип | Размер плит | Размер пресс-формы | Производственный цикл | Мощность | |||||
Винтовые (механические) | ||||||||||
EPS-C-0907 | Винтовой (механ.) | 900х700 мм | 750х600 мм | 60~120 сек. | 1.5 кВт | |||||
EPS-C-1090 | Винтовой (механ.) | 1000х900 мм | 800х800 мм | 70~140 сек. | 1.8 кВт | |||||
EPS-C-1210 | Винтовой (механ.) | 1200х1000 мм | 1000х800 мм | 80~150 сек. | 2.2 кВт | |||||
EPS-C-1310 | Винтовой (механ.) | 1300х1000 мм | 1100х900 мм | 90~180 сек | 3.0 кВт | |||||
EPS-C-1512 | Винтовой (механ.) | 1500х1200 мм | 1300х1100 мм | 100~190 сек. | 4.5 кВт | |||||
Гидравлические | ||||||||||
LWH-1210 | Гидравлический | 1200х1000 мм | 1000х800 мм | 70~140 сек. | 5.5 кВт | |||||
LWH-1412 | Гидравлический | 1400х1200 мм | 1200х1100 мм | 80~160 сек. | 7.5 кВт | |||||
LWH-1513 | Гидравлический | 1500х1300 мм | 1300х1200 мм | 90~180 сек. | 8.5 кВт | |||||
LWH-1814 | Гидравлический | 1800х1400 мм | 1600х1300 мм | 100~200 сек. | 11 кВт |
"ЧЕРНЫЙ ЦЕХ" - формовка и заливка модельных блоков ЛГМ
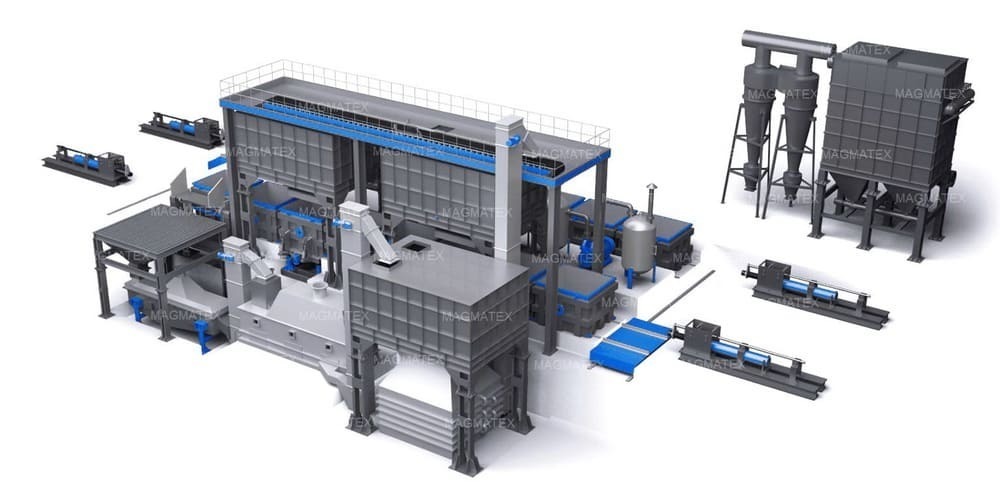
Технологические операции: Формовка модели в опоке → Заливка модели → Выбивка остывшей модели → Регенерация отработанного песка
Трехмерный вибростол XYZ
Трехмерный вибростол XYZТрехмерный вибростол предназначен для уплотнения основного объема песка, засыпаемого в вакуумную опоку после установки модельных блоков. Вибростол состоит из стационарной части, рабочей части, амортизаторов, вибродвигателей и пневматических фиксаторов. Вибрация производится за счет шести асинхронных вибродвигателей, вращающихся в противоположных направлениях. При работе пневматические захваты фиксируют опоку на рабочей части. После засыпки песка включаются вибродвигатели. Вибрация направлена по оси X, Y, Z. Вибростол двухмерный предназначен для уплотнения песчаной подушки в вакуумной опоке перед установкой моделей.
- XYZ-I г/п 5 т., размеры вибростола 1200x1200x750 мм, максимальные размеры опоки 1000х1000х1500 мм
- XYZ-II г/п 8 т.,размеры вибростола 1500х1500х750мм, максимальные размеры опоки 1300х1300х1800 мм
- XYZ-IIIг/п 12 т., размеры вибростола 1800х1800х750мм, максимальные размеры опоки 1600х1600х2200 мм
- XYZ-IV г/п 20 т., размеры вибростола 3000х2100х750 мм, максимальные размеры опоки 2800х1900х2500 мм
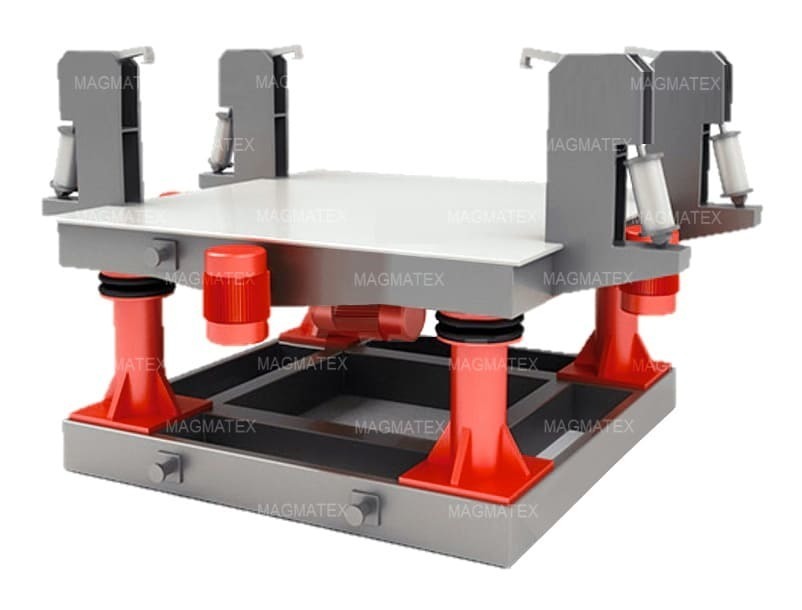
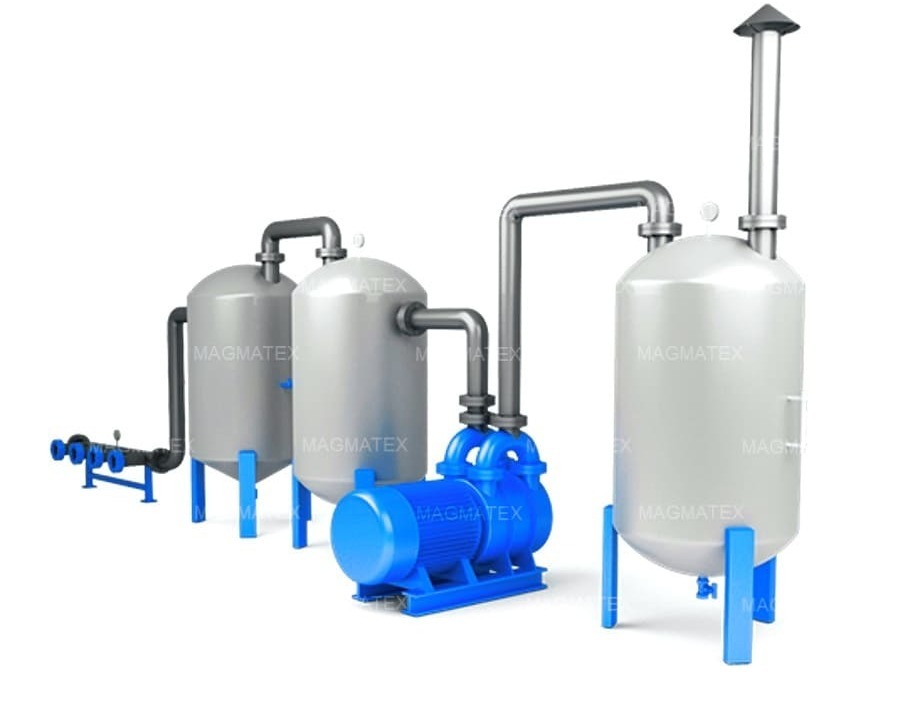
Вакуумная система линии ЛГМ
Вакуумная система служит для создания отрицательного давления (разряжения) в вакуумной опоке. Основные части системы - водоциркуляционный вакумный насос, ресивер, клапаны, пылеуловитель, сепаратор, гребенка с резиновыми армированными рукавами. Из бака воды открытием соответствующих кранов заполняются на половину емкости сепаратора и мокрого пылеуловителя.
При работе насоса осуществляется циркуляция воды от емкости сепаратора до насоса и обратно в сепаратор. Воздух непрерывно откачивается из опок. При этом мелкая фракция, прошедшая сквозь мелкую сетку опоки, осаживается в воде пылеуловителя.
Вакуумный ресивер аккумулирует отрицательное давление, что позволяет поддерживать разряжение даже при выключенном насосе. Если опока герметична, а пленка на песке лежит ровно, то ресивер позволит удерживать уровень разряжения еще несколько минут.
Модель SK-12: производительность 12 м3/мин, расход воды 40-50 л/мин, мощность 18,5 кВт
Модель SK-20: производительность 20 м3/мин, расход воды 60-80 л/мин, мощность 30 кВт
Модель SK-30: производительность 30 м3/мин, расход воды 70-100 л/мин, мощность 55 кВт
Модель SK-40: производительность 40 м3/мин, расход воды 80-115 л/мин, мощность 75 кВт
Вакуумная опока
Вакуумная опока - сварной стальной короб, который используется при формовке пенополистирольных блоков, засыпаемых песком определенной фракции. Стенки и днище опоки имеет вакуум-проводы, обеспечивающие равномерное разряжение.
Окрашенный модельный блок устанавливается на расстоянии не менее 50~70 мм от стенок опоки и днища. Заполненные песком вакуумные опоки перемещаются на трехмерный вибростол, включаются вибродвигатели и производится уплотнение по всему объему (по оси X-Y-Z). После виброуплотнения опока накрывается пленкой, присыпается песком и подключается резиновыми рукавами к вакуумной системе.Опоки проектируются в соответствии с требованиями Заказчика. После виброуплотнения опока накрывается пленкой, присыпается песком и подключается резиновыми рукавами к вакуумной системе.
Опоки проектируются в соответствии с требованиями Заказчика.
- Размер опоки 1000х1000х1000 мм, масса песка в опоке 1600 кг, размеры вибростола 1200x1200x750 мм
- Размер опоки 1500х1000х1000 мм, масса песка в опоке 2400 кг, размеры вибростола 1500х1500х750 мм
- Размер опоки 2000х1500х1500 мм, масса песка в опоке 7200 кг, размеры вибростола 1800х1800х750 мм
- Размер опоки 3000х1500х1500 мм, масса песка в опоке 10800 кг, размеры вибростола 3000х2100х750 мм
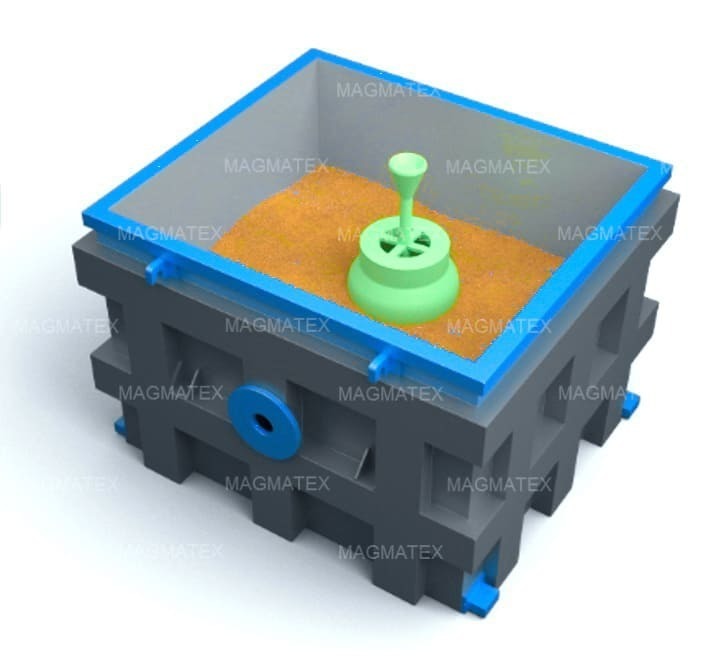
Система пескооборота формовочной линии ЛГМ
Рабочий бункер системы пескооборота линии ЛГМ.
Формовка моделей в вакуумной опоке ЛГМ
Заливка вакуумных опок по технологии ЛГМ
Просыпная решетка предназначена для разделения отливок и песка. Она представляет собой раму, закрепленной на фундаменте. Просыпная решетка идет в комплексе с приёмным бункером, который оснащён пневматическим шиберном. Пневматический шибер, предназначен для запирания приемного бункера просыпной решетки. Поток песка регулируется ручной заслонкой. Открытие шибера происходит за счет подачи на пневмоцилиндр сжатого воздуха.
Виброгрохот, предназначен для просеивания отработанного песка и транспортирования его до цепного элеватора. Виброгрохот состоит из стационарной части, подвижной части, вибродвигателей, пружин, сита и пр. Внутри виброгрохота смонтирован трубчатый теплообменник, по которому циркулирует вода. Частицы краски с отливок, крупные включения и скрап проходят через отверстия просыпной решетки и попадают на сито виброгрохота. Они движутся по ситу и разгружаются по отдельному желобу в установленную тару. Просеянный песок, пройдя сито, разгружается в нижнюю головку элеватора для подъема. В месте пересыпки устанавливается вытяжной зонт для отвода пылевидной фракции. Вибрация генерируется двумя асинхронными вибродвигателями, вращающимися в разных направлениях. Вибродвигатели установлены под углом к оси горизонта, что обеспечивает направленное движение песка и отсеянных включений.
Шкаф охлаждения служит для охлаждения и обеспыливания отработанного песка. Шкаф состоит из воздуходувки, распределителя, клапанов, трубчатого теплообменника корпуса и пылеулавливающего зонта. Загрузка песка осуществляется через верхний патрубок, воздуходувкой нагнетается в нижний слой избыточное воздушное давление, уровень дутья в нижнем слое регулируется клапаном-бабочкой, расположенных на распределителе воздушного потока. Внутри шкафа смонтирован трубчатый водоохлаждаемый теплообменник. Благодаря избыточному воздушному давлению в нижней части шкафа возникает эффект «кипения» песка (кипящий слой), мелкая фракция и частицы пыли имеют меньшую массу, поэтому поднимаются на большую высоту и удаляются в систему пылеулавливания. Песок находясь в непрерывном движении, соприкасается с трубчатым теплообменником и отдает ему часть тепла. Таким образом, происходит обеспыливание и охлаждение песка. Охлажденный и обеспыленный песок самотеком разгружается через разгрузочный желоб. Шкаф охлаждения – важный узел в системе регенерации. Для периодической очистки шкафа предусмотрены окна.
Система пылеудаления, предназначена для улавливания пыли и мелкой фракции отработанного песка из основного объема песка. Система пылеулавливания состоит из картриджного пылеуловителя, трубопроводов, клапанов-бабочек, вытяжного вентилятора, импульсной системы продувки, разгрузочного шнека и пр. При работе системы запыленный воздух откачивается от узлов линии и собирается в единый трубопровод, направленный к пылеуловителю. Для регулировки вытяжной вентиляции на каждом устройстве предусмотрены клапана-бабочки. Запыленный воздух проходит через картриджный пылеуловитель сверху вниз, пыль оседает на стенках картриджа, а очищенный воздух собирается в единый патрубок, направленный к вытяжному вентилятору .
Пылеуловитель имеет функцию очистки методом обратной продувки. Для этих целей сам объем картриджного пылеуловителя разбит на секции. При отключении вытяжного вентилятора становится возможной очистка пылеуловителя. Для этого секции пылеуловителя закрываются секционными клапанами, запускается импульсный клапан очистки, запускается импульсная воздуходувка, после чего секционные клапана поочередно открываются.